Wear resistant hard alloy coatings parts based on tungsten carbide, chromium carbide
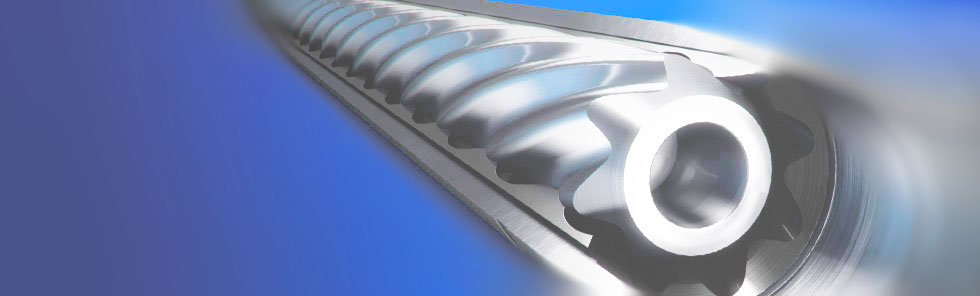
For more than 20 years, our company has been specializing in applying special wear-resistant coatings by gas thermal methods to the metal surfaces of submersible equipment. Hard alloy protective coatings have significant advantages over electroplating, which allows to increase the reliability of operation and reduce the cost of production and service of submersible and other types of oil and gas equipment.
Gas-thermal wear-resistant coatings TSPС:
- improved performance;
- increase the service life of parts and assemblies by 3 times;
- contribute to an increase in the inter-repair period (MCI) of equipment by preventing various types of corrosion: general, spots, in the form of a plateau, pitting, contact, grooves and mayse corrosion;
- due to increased corrosion resistance of articles, coefficient of friction is reduced and, as a result, setting is prevented.
We strengthen new blades by surfacing and restore worn-out centralizers and calibrators, as well as repair of wear-resistant platforms of the rock resistance recorder (resistivimeter):
- Import substitution;
- Maintainability;
- Reducing the delivery time of parts from the manufacturer to the operator;
- Lower costs for the purchase of expensive new equipment;